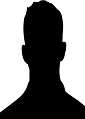
Woo-Gwang Jung
Kookmin University, Korea
Title: Optimization of process for the production of glass-ceramic material recycled from steel industry slags and some waste
Biography
Biography: Woo-Gwang Jung
Abstract
A large amount of slag is generated in the steel product production process. In general, it is known that about 300 kg of blast furnace slag is produced for 1 ton of pig iron, and about 25 million tons of steel slag is generated annually in Korea. Steel slag can be classified into blast furnace (BF) slag and steel making slag. Blast furnace slag accounts for about 60% of all steel slag. It is widely used as cement raw material and used as civil engineering and construction materials. However, steelmaking slag has a high basicity and its utilization is restricted due to the pulverization behavior due to hydration reaction. Therefore, the recycling rate is limited to be about 20%, and the rest is accumulated in the factory or landfilled, causing environmental problems. This is becoming burdensome in steel industry. Therefore, it is one of the most important tasks to develop appropriate applications that can recycle steelmaking slag and increase added value. In this study, Fe-Ni slag, converter slag and dephosphorization slag generated from steel industry, and fly ash or bottom ash from a power plant were mixed in appropriate mixing ratio, and melted in a melting furnace on mass-production process for glass ceramics. Then the glass-ceramic products having basalt composition with SiO2, Al2O3, CaO, MgO, Fe2O3 components were fabricated through casting and heat treatment process. The comparison was made for the samples before and after the modification of process condition. Glass-Ceramic samples before and after the process modification were similar in chemical composition, but Al2O3 and Na2O contents were slightly higher in the samples before the modification. Before and after the process modification, it was confirmed that the sample had a melting temperature below 1250 oC, and the pyroxene and diopside are the primary phases in the product. The crystallization temperature in sample after modification was found to be higher than that in sample before modification. The activation energy for crystallization was evaluated as 467 kJ/mol of the sample before the process modification, and 337 kJ/mol of the sample after the process modification. The degree of crystallinity was evaluated as 82% before the process change and 87% after the process change, respectively. Mechanical properties such as compressive strength and bending strength were evaluated as excellent for the sample after the process modification. Optimized process for the production of glass-ceramic materials from steel industry slags and industrial waste was deduced through the evaluation of properties, facility modification and process control.