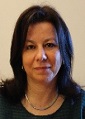
Helena Maria Vieira Monteiro Soares
University of Porto, Portugal
Title: A nearly closed environmental friendly process for recovering metals with high yield and purity from spent hydrodesulphurization catalysts
Biography
Biography: Helena Maria Vieira Monteiro Soares
Abstract
HDS catalysts are extensively used in the petroleum refining industry. When they can no longer be used, the catalysts become solid wastes (around 120,000 tons per year are produced), which are classified as hazardous materials. The present work was centered in the recovery of Ni and Mo from a spent Ni-Mo catalyst and subsequent separation steps in order to recovery each metal with high yield and purity. The HDS catalyst was initially roasted and chemically characterized (12.1, 30 and 2.6% of Mo, Al and Ni, respectively). Then, the leaching of Mo and Ni was studied using a microwave assisted method in two subsequent independent stages: The first to recover Mo using an alkaline (NaOH) leaching and the second to recover Ni using acid (H2SO4) leaching. Results were compared with a conventional leaching procedure. Microwave assisted leaching led to better extraction efficiencies (89% of Mo and >90% of Ni for alkaline and acid leaching, respectively) and selectivity (only in the case of the alkaline leaching, where Al dissolution was only 6%) and lower heating times. Recovery of Mo from the alkaline leachate was achieved by precipitation in the form of SrMoO4 (96% of yield with 99% of purity). Molecular recognition technology, using SuperLig® 167 resin, enabled an easy and efficient separation of the metals (Ni, Mo and Al) present in the H2SO4 leachate into mono-metal solutions (Al in the raffinate, Mo and Ni in the alkaline and acid eluates, respectively) with high yield (99.7, 100 and 87% respectively) and purity (99.3, 99.8 and 98.7% respectively).